Expansion Flange: Managing Thermal Expansion in Piping Systems
In industrial piping systems, temperature fluctuations can cause expansion and contraction of the pipes, leading to stress and potential damage. To mitigate these issues, expansion flanges are utilized. These specialized flanges provide flexibility and allow for controlled movement, effectively managing thermal expansion and contraction. This article explores the significance of expansion flanges, their purpose, types, and benefits in maintaining the integrity of piping systems.
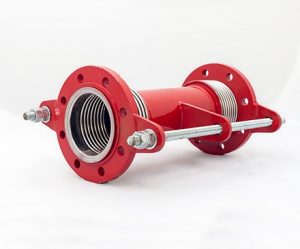
Understanding Expansion Flanges
Expansion flanges, also known as expansion joints or compensators, are mechanical devices installed in piping systems to accommodate thermal expansion and contraction. They are designed to absorb the dimensional changes resulting from temperature variations, preventing excessive stress and potential damage to the pipes and associated equipment. Expansion flanges are particularly crucial in systems where high temperatures, such as in steam or thermal oil applications, are involved.
Purpose and Types of Expansion Flange
The primary purpose of expansion flanges is to provide flexibility and absorb movement caused by thermal expansion. They compensate for the changes in pipe length, relieving stress and strain on the piping system. There are various types of expansion flanges available, including:
Bellows Expansion Flanges: These flanges utilize a flexible bellows element that expands and contracts to accommodate pipe movement. Bellows are typically made of materials such as stainless steel or rubber, depending on the application.
Gimbal Expansion Flanges: Gimbal flanges consist of two rotatable hinges that allow for angular movement. They are suitable for systems where angular displacement is expected, such as pipelines connected to rotating equipment.
Hinged Expansion Flanges: Hinged flanges have a single pivot point, allowing for angular movement in a specific direction. They are commonly used in applications where only one plane of movement is required.
Slip Expansion Flanges: Slip flanges provide axial movement without angular rotation. They consist of two flange sections connected by a sliding mechanism, enabling pipe expansion and contraction.
Benefits of Expansion Flanges: Expansion flanges offer several key benefits in piping systems:
- Stress Reduction: By absorbing thermal expansion and contraction, expansion flanges help reduce stress on the pipes, fittings, and equipment connected to the system. This helps prevent damage and prolongs the service life of the overall system.
- Enhanced System Integrity: By accommodating movement and minimizing stress, expansion flanges contribute to the overall integrity of the piping system. They help prevent leaks, cracks, and failures that can occur due to thermal expansion-related stresses.
- Noise and Vibration Reduction: Expansion flanges can help reduce noise and vibration caused by the movement of pipes. By absorbing the energy generated during expansion and contraction, they minimize the transmission of vibrations and noise throughout the system.
- Maintenance and Repair Facilitation: The use of expansion flanges simplifies maintenance and repair tasks by allowing for easy removal and replacement of sections of piping. This helps minimize downtime and improves system accessibility for maintenance personnel.
Installation and Maintenance
Proper installation and regular maintenance are crucial for the optimal performance of expansion flanges. During installation, factors such as proper alignment, correct anchoring, and sufficient clearance for movement must be considered. Regular inspections should be conducted to check for signs of wear, damage, or leaks in the expansion flanges. Additionally, the system’s operating conditions, including temperature and pressure, should be monitored to ensure that the expansion flanges are appropriately sized and rated for the application.
Conclusion: Expansion flanges play a vital role in managing thermal expansion and contraction in industrial piping systems. By providing flexibility and accommodating movement, these flanges help prevent stress, damage, and potential failures. The selection and installation of the appropriate type of expansion flange for specific applications are essential to ensure the integrity and reliability of the piping system.